Non-isolated DC-DC Buck-Boost Converter Buying Guide
A buck-boost DC-DC converter is a type of switching power supply that can either step up (boost) or step down (buck) input voltage to produce a desired output voltage. Non-isolated DC buck-boost converters are characterized by their lack of galvanic isolation between the input and output, which means the input and output share a common ground. Non-isolated buck-boost converters are widely used in applications like battery-powered systems, automotive electronics, and renewable energy systems due to their ability to handle varying input voltages.
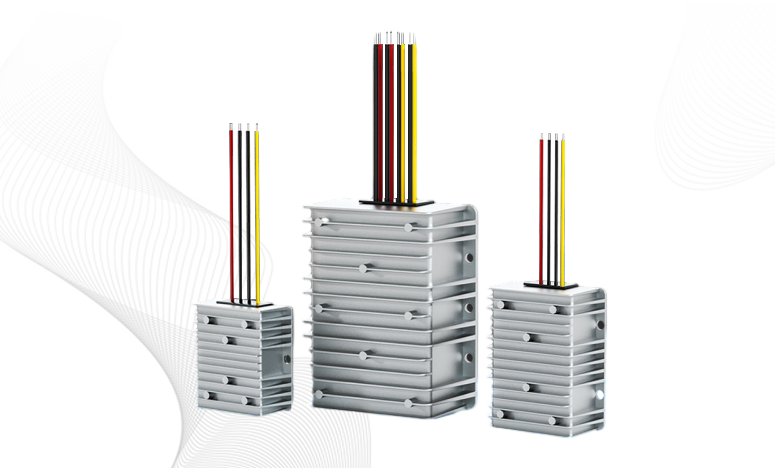
Buck-Boost Converter Working Principle
Non-isolated buck-boost modules work by controlling the duty cycle of a switch, often a MOSFET or IGBT, which alternates between on and off states. In the buck mode, the converter steps down the input voltage when it's above the required output voltage, while in boost mode, it steps up the voltage when the input is below the required output voltage. These converters typically operate in two primary modes: Continuous Conduction Mode (CCM) and Discontinuous Conduction Mode (DCM), affecting efficiency and performance.
- CCM: The inductor current never reaches zero during the switching cycle, reducing current ripple.
- DCM: The inductor current drops to zero within each cycle, which can simplify control circuitry but may introduce more noise and ripple.
Key Parameters to Consider
When selecting a non-isolated DC-DC buck-boost converter, understanding the parameters that impact performance and compatibility is essential. Here are some of the most critical parameters to consider:
- Input Voltage Range: Define the minimum and maximum input voltages based on the power source and application. The selected converter should support the entire input range, as a mismatch can cause under-voltage or over-voltage issues, potentially leading to device failure.
- Output Voltage Range: The required output voltage range is crucial, especially in systems with precise voltage requirements. A wider range can accommodate applications where load demands change over time, such as adjustable or programmable power supplies.
- Output Current Capability: The converter must provide sufficient current for the load. Exceeding the current rating can damage components and reduce efficiency. Applications requiring high current should look for converters with built-in current limiting to avoid damage under heavy loads.
- Switching Frequency: Higher switching frequencies enable smaller inductors and capacitors, reducing size and weight. However, higher frequencies can increase switching losses and reduce efficiency. Typical switching frequencies range from 100 kHz to 2 MHz, with some converters reaching even higher frequencies for compact designs.
- Efficiency: Efficiency is crucial for applications where power conservation is critical, such as battery-powered devices. Non-isolated buck-boost converters can achieve efficiencies from 80% to 95%, but this depends on the load, switching frequency, and duty cycle. Consider DC DC converters with synchronous rectification for improved efficiency.
- Thermal Performance: High efficiency reduces thermal losses, but the converter's design and ambient conditions affect temperature rise. Selecting a converter with good thermal management, such as a heat sink or thermal shutdown protection, is important for high-power applications.
- Package and Size: Physical size can be a constraint in compact electronics, where the overall solution footprint and layout are critical. Modules with integrated components can help reduce size, but ensure adequate thermal design if using a compact solution.
- Control Method: Different control methods like pulse-width modulation (PWM) or pulse-frequency modulation (PFM) impact the converter’s efficiency and noise characteristics. PWM is commonly used for stable output, while PFM can offer improved efficiency at light loads.
Selection Guide by Application
Different applications have specific needs. Here’s a breakdown of common requirements and suggested features based on use cases:
Battery-Operated Devices (e.g., Smartphones, Tablets):
- Input Voltage: Should support a wide range due to battery discharge.
- Efficiency: High, especially in light load conditions.
- Size: Compact solutions are preferred.
- Control: Look for PFM control for better efficiency at light loads.
Automotive Electronics:
- Input Voltage Range: 12-24V, with high tolerance for spikes and surges.
- Thermal Management: Necessary for operation in a high-temperature environment.
- EMI Consideration: Important for compliance with automotive standards.
- Robust Protection: Over-voltage, over-current, and thermal protection are crucial.
Industrial Applications (e.g., Sensors, Actuators): Reliability:
- Prioritize long lifecycle and robust protection features.
- Output Stability: Low ripple and accurate voltage regulation are essential.
- Packaging: Encapsulated or rugged packaging for harsh environments.
Renewable Energy Systems (e.g., Solar Panels, Wind Turbines):
- Wide Input Range: To accommodate variable input voltages from renewable sources.
- High Efficiency: Essential to maximize energy harvesting.
- MPPT Compatibility: If integrated with solar systems, look for MPPT support to maximize power output.