How to Choose a DC-DC Power Converter?
In the world of electronics and power management, selecting the right DC-DC power converter is crucial for the efficiency, reliability, and longevity of any device or system. DC-DC converters are used in applications ranging from simple gadgets to complex industrial equipment, allowing for the smooth transformation of voltage levels to meet various power requirements. Here's a guide to help you make the right choice.
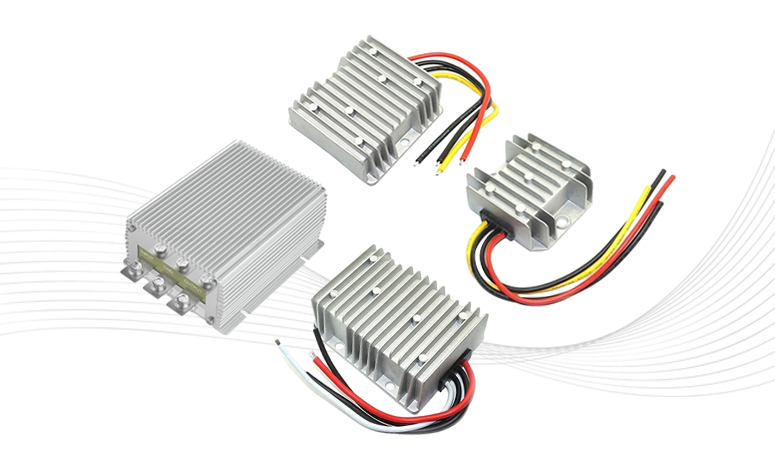
1. Understand the Basics of DC-DC Converters
DC-DC converters are electronic devices that transform a DC input voltage to a different DC output voltage. The two primary types are:- Non-isolated Buck Converters: Step down the input voltage.
- Non-isolated Boost Converters: Step up the input voltage.
- Non-isolated Buck-Boost Converters: Can both step up and step down the voltage.
2. Define the Input and Output Requirements
The first step is to specify both input and output requirements:- Input Voltage Range: Determine the minimum and maximum input voltage. This range helps identify converters capable of handling fluctuations in the power source.
- Output Voltage: Know the exact voltage your device needs. For example, if you're powering a 5V circuit from a 12V battery, you'll need a buck converter.
- Output Current: The current demand is another essential factor. Knowing the maximum current the load will draw helps in selecting a converter with the correct current rating.
3. Calculate Power and Efficiency Needs
High-efficiency converters are essential in applications where power conservation is critical, such as in battery-operated devices. A high-efficiency converter minimizes energy losses as heat and extends battery life.
To calculate efficiency: Efficiency = Output Power / Input Power × 100%
Higher efficiency reduces thermal management requirements, helping avoid extra costs for heat sinks or cooling systems.
4. Consider the Switching Frequency
The switching frequency affects both the size of the converter and its efficiency. Higher switching frequencies allow for smaller inductors and capacitors but can lead to increased switching losses, impacting efficiency. Lower frequencies, conversely, reduce switching losses but require larger components, impacting the size.
When choosing a switching frequency, consider:
Size Constraints: If space is limited, higher frequencies may allow for a more compact design.
Thermal Management: If efficiency is paramount, consider a moderate frequency to balance component size and thermal losses.
5. Review the Thermal Management Requirements
Thermal performance is crucial, especially in high-power applications. Check the power dissipation rating, which shows how much heat the converter will generate under full load. Converters with integrated heat sinks or fans are often used in high-power systems, while lower-power systems might only require passive cooling.Additionally, be mindful of the environment in which the converter will operate. High ambient temperatures may necessitate additional cooling.
6. Check for Voltage Regulation and Ripple Requirements
A good DC-DC converter should have stable voltage regulation to maintain a consistent output even when the input fluctuates or the load changes. Ripple and noise are also essential factors, particularly in sensitive electronic applications. Look for:- Low Output Ripple: Excessive ripple can disrupt sensitive devices, particularly in communication and audio equipment. Regulation Precision: Ensure the converter maintains its output voltage within an acceptable range under varying load and input conditions.
7. Review Safety and Protection Features
- Converters often come with built-in safety features that protect both the converter and the device it powers. These include: Overcurrent Protection (OCP): Prevents damage from excessive current draw.
- Overtemperature Protection (OTP): Shuts down the converter if it overheats.
- Short Circuit Protection: Stops current flow during a short circuit.
- Overvoltage Protection (OVP): Prevents the output voltage from exceeding safe limits. For battery-powered applications, look for converters with Undervoltage lockout (UVLO) to protect against deep discharges.
8. Evaluate Physical Size and Form Factor
In compact systems, the size of the converter can be a limiting factor. Fortunately, manufacturers offer a variety of form factors, from modules to surface-mount packages. For portable applications, opt for small, lightweight converters, while stationary or industrial setups may have more flexibility for larger designs.
9. Assess Cost Versus Performance Needs
High-performance DC-DC converters with advanced features may be costly, so it's essential to strike a balance between cost and required performance. If your application doesn't need extremely tight regulation or high efficiency, a simpler, more cost-effective converter might suffice.
10. Consider the Manufacturer and Support
Selecting a converter from a reputable manufacturer ensures reliability, as these companies typically offer thorough documentation, testing, and support. Look for providers with good customer support, and if your application is critical, consider selecting components that meet certifications (e.g., ISO, RoHS).
Choosing a DC-DC power converter is a nuanced process. By carefully analyzing your requirements—from input/output voltage to efficiency, size, and safety features—you can find the right converter that meets both your performance and budget needs. Whether powering a simple device or a sophisticated industrial system, the right DC-DC converter can significantly enhance overall reliability and efficiency.