How Does a DC-DC Converter Work?
A DC-DC power converter is an electronic device that transforms direct current (DC) voltage levels, either stepping up (boosting) or stepping down (buck) the voltage to suit various applications. These converters play a vital role in many systems where different voltage levels are required for various components, and they ensure energy-efficient power management in industries, including automotive, industrial automation, consumer electronics, and renewable energy.
Buck boost converters are particularly important in portable electronics where battery power needs to be optimized for different components with varying voltage requirements. DC-DC converters are also used in electric vehicles, industrial equipment, and photovoltaic systems. They provide the flexibility to step up or step down voltages as needed, which makes them versatile for a broad range of applications.
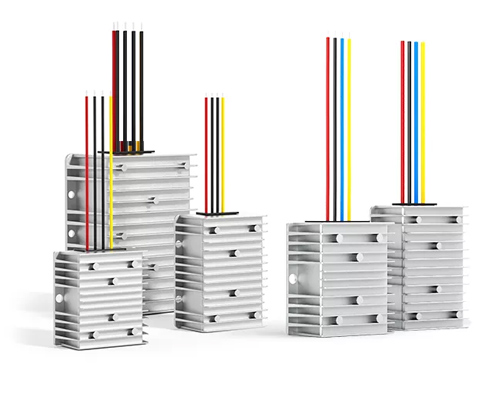
Types of DC-DC Converters
- Non-isolated DC-DC Buck Converter (Step-Down)
- Non-isolated DC-DC Boost Converter (Step-Up)
- Non-isolated DC-DC Buck-Boost Converter
- Isolated DC-DC Converter
Each converter has a unique design and operational principle to achieve different objectives, from voltage regulation to isolation and efficiency optimization.
Key Components in DC-DC Converters
While the configuration and components can vary based on the type of DC-DC converter, some essential components are present in most designs:
- Inductor: An inductor is a coil of wire that resists changes in current. It stores energy in the form of a magnetic field when current flows through it and releases it when the current decreases. Inductors are crucial in storing and transferring energy in switching converters.
- Capacitor: Capacitors store energy in an electric field, which helps smooth the output voltage and reduce ripple.
- Switches: Power transistors, such as MOSFETs or IGBTs, are commonly used as switches in converters. They switch on and off rapidly to control the flow of energy and adjust the output voltage.
- Diode: Diodes are used in converters to direct the current flow and prevent backflow, ensuring that current flows in a single direction.
- Control Circuit: A control circuit modulates the duty cycle or frequency of the switch, enabling the converter to adjust the output voltage in response to changes in load or input voltage.
Basic Working Principle of DC-DC Converters
1. Buck Converter (Step-Down Converter)
A buck converter is designed to reduce (or step down) the input voltage to a lower output voltage. Here’s how it works:
- Switching: A transistor (often a MOSFET) acts as a switch that controls the input voltage. When the switch is on, current flows through an inductor, storing energy.
- Inductor and Capacitor: When the switch turns off, the inductor resists the sudden change in current by releasing the stored energy, maintaining current flow. The energy is then directed to the load via a diode and filtered by a capacitor to smooth out the output voltage.
- Control Circuitry: The output voltage is regulated by controlling the duty cycle—the percentage of time the switch is on versus off. A higher duty cycle increases output voltage, while a lower duty cycle decreases it.
The buck converter is highly efficient because it minimizes energy losses during switching. Applications include battery-operated devices and any circuits where stable low voltage is required from a higher input.
2. Boost Converter (Step-Up Converter)
A boost converter raises (or steps up) the input voltage to a higher output voltage. It operates as follows:
- Switching: Initially, the switch (transistor) is turned on, allowing current to pass through the inductor. During this time, the inductor stores energy in a magnetic field.
- Energy Release: When the switch is turned off, the magnetic field collapses, releasing the stored energy. This forces current through the diode to the output, combining with the input voltage to produce a higher output voltage.
- Duty Cycle Control: By adjusting the duty cycle, the boost converter controls the output voltage, ensuring a stable output. The longer the switch remains on, the greater the amount of energy stored, resulting in a higher output voltage.
Boost converters are commonly used in situations where a higher voltage is needed from a lower voltage source, such as in renewable energy systems (solar panels), automotive systems, and battery-powered electronics.
3. Buck-Boost Converter
A buck-boost converter is a versatile type that can either step up or step down the input voltage, depending on the requirements. This converter is used where input voltage may vary widely and may need to be increased or decreased to match a fixed output requirement.
- Switching and Inductor Storage: The switch is controlled by a duty cycle that determines whether the circuit acts as a step-up or step-down converter. When the switch is on, the inductor stores energy.
- Polarity Reversal: Unlike buck and boost converters, the buck-boost design reverses the output voltage polarity, making it suitable for certain applications where negative voltage is required.
- Duty Cycle Variation: If the duty cycle is less than 50%, the converter steps down the voltage; if it’s greater than 50%, it steps up.
Buck-boost converters are commonly used in power supplies where output voltage stability is critical, such as in battery management systems.
4. Isolated DC-DC Converters (Flyback and Forward Converters)
Isolated converters are used in applications where electrical isolation is needed between input and output, such as in medical devices and communication systems.
- Flyback Converter: The flyback power converter is a popular isolated converter that uses a transformer to transfer energy. When the switch is on, energy is stored in the transformer's core. When the switch turns off, the stored energy is released to the secondary side and the load. This design provides both voltage conversion and isolation.
- Forward Converter: The forward converter also uses a transformer, but it differs from the flyback converter by directly transferring energy to the secondary side when the switch is on. When the switch turns off, the energy is supplied to the load through the output inductor and diode.
Efficiency and Control in DC-DC Converters
High efficiency is one of the primary goals in DC-DC converter design, particularly for battery-powered applications. Modern buck boost converters often achieve efficiencies over 90% due to low-loss components and advanced control techniques. Pulse Width Modulation (PWM) is widely used in converters to control the duty cycle and hence the output voltage. For higher efficiency at light loads, many converters also implement Pulse Frequency Modulation (PFM), which adjusts the frequency of switching to reduce losses.